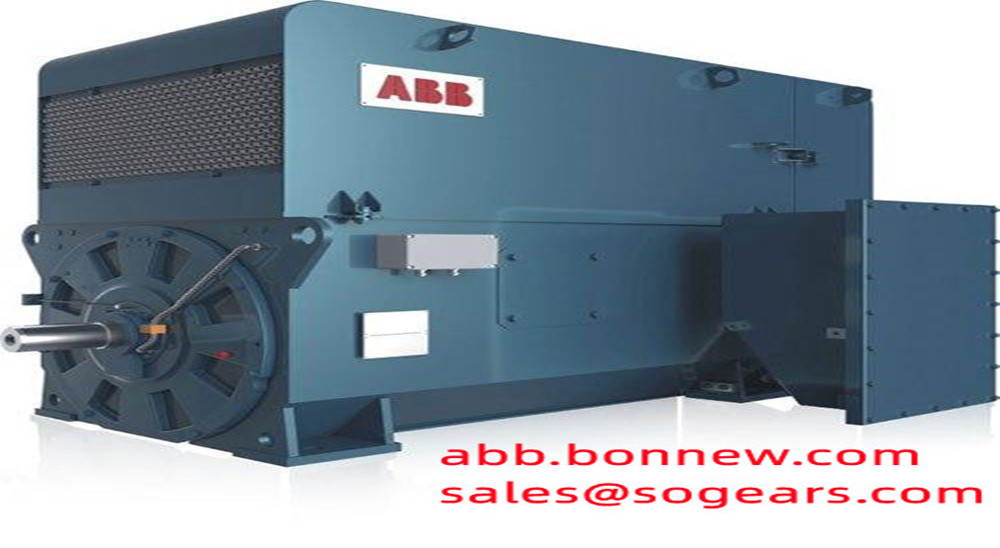
Products: rich and comprehensive, quality first
Without motors, there would be no modern industry. One of the core businesses of ABB, a global leader in power and automation technology, is motors. ABB Motors settled in Shanghai in 1995, and successively established Shanghai ABB Motor Co., Ltd. and ABB High Voltage Motor Co., Ltd. Over the past 20 years, from the simple introduction and sales of foreign products, a local motor R&D team has been gradually established. While continuously localizing products, it is also actively carrying out independent research and development of local products.
Yao Yedong, head of ABB Motors and Generators China market and sales, said that after years of painstaking research, ABB Motors has thoroughly penetrated into major sub-application fields, such as the compressor industry, and has a full range of product solutions: for screw compressors Low-voltage M3 series motors and permanent magnet motors for medium-sized compressors, high-voltage modular motors NMI and AMI series for medium-sized compressors, and synchronous motors AMS series for large-scale compressors and AMI series for frame sizes above 710.
Not only that, for key customers, ABB has also completed the standardized design of a full range of products to meet customers' special requirements in terms of process and delivery time. In the application of high-flow compressors, ABB's synchronous motor products have always been characterized by high efficiency and high power factor, and have a good reputation for providing stable and reliable fluid equipment production lines for owners. For customers' new compressor products in the R&D stage, ABB can also provide comprehensive technical support to escort product R&D.
As we all know, the application of compressor drive motor is a highly customized field. Major mainstream compressor manufacturers have their own specifications. The launch of a complete range of products from ABB motors is inseparable from the support of a professional team. Therefore, ABB has set up a technical team dedicated to compressor applications a long time ago. Through long-term cooperation and cooperation with major international compressor manufacturers, ABB has continuously improved its professional capabilities in this application field. At present, the technical team has accumulated more than ten years of compressor application experience, has a full understanding of customers' regular needs, and can also respond quickly and provide feedback to customers' special needs. In the application of large-flow compressors, such as Ningbo Zhenhai Refinery Linde Gas-Air Separation Project, the target production capacity of the air separation unit is 80,000 cubic meters per hour, the equipment investment is high, and the reliability and stability of the equipment are extremely high. By providing highly customized design solutions, the synchronous motor not only achieves high efficiency of 98.67% and 98.36%, but also can achieve soft start even in areas with weak power grids through variable frequency drive, thereby reducing the impact on the power grid and equipment. product reliability and stability.
Technology: keep the original intention, professional and reliable
In addition to rich product solutions in the compressor industry, ABB motors pay more attention to the control of energy efficiency. In recent years, with the development of the market, the compressor industry has raised its attention to energy efficiency to an unprecedented height, and many brands have been striving for the super-first-class energy efficiency of the full range of products. The new energy efficiency level standard GB19153-2019, which will be implemented from July 2020, not only puts forward higher requirements for the energy efficiency of the compressor as a whole, but also the detection method is closer to the actual use situation. The new standard uniformly upgrades GB's requirements for energy efficiency, which is a state's attitude towards sustainable development. ABB is naturally responding to the country's call to support the improvement of energy efficiency in the compressor industry with better motor product technology.
At present, ABB's full range of products can meet the energy efficiency requirements of all applications in the market. For high-voltage products, it has launched high-voltage modular AMI and NMI series that meet the national GB1 and GB2 requirements; for the special needs of centrifugal compressors themselves - low Vibration and low noise, AMI and NMI can also fully meet customer requirements to achieve B-level vibration and low-noise design; new GB energy efficiency requirements for motors for screw compressors (GB18613-2020 "Energy Efficiency Limits and Energy Efficiency Levels for Electric Motors") It will be officially implemented in June 2021. ABB has taken a step ahead of the new specification, and has products that respond to the new GB energy efficiency in both traditional motors and special permanent magnet motors. In terms of traditional motors, ABB mainly promotes the M3 series, which can meet all mainstream energy efficiency requirements including GB1, and IE4 products are also preparing for localization.
It is worth mentioning that ABB has developed a customized low-voltage permanent magnet synchronous motor by combining the R&D and production experience accumulated in the field of low-voltage permanent magnet motors over the years, which can achieve IE4/IE5 ultra-high energy efficiency and ultra-high energy efficiency. Energy efficiency, power saving effect is very obvious. Compared with asynchronous motors with the same torque output, the volume can be reduced by 1 to 2 frame sizes, and the weight can be reduced by 40% to 60%. In addition, ABB's Micaduar insulation system, simulation calculation of motor performance and basic application and forward-looking research, including exchanges and cooperation on a global scale, can ensure the technical advantages of ABB products.
It is true that from different standpoints, compressor manufacturers and end users have different focuses on each element of the supporting motor. For example, for the manufacturer, the excellent performance of the motor and the continuous and stable long-term operation are the focus of the investigation, and the end user not only pays attention to the above two points, but also pays great attention to the price of the product. However, in the face of increasingly fierce market competition, ABB has always maintained its original intention, insisted on quality first, and wholeheartedly provided customers with better solutions. ABB has always believed that quality is the cornerstone of a brand. Compared with the overall low price of the compressor, especially for customers who pay attention to the one-time purchase price, the price of ABB's motors is indeed not competitive. However, the one-time purchase cost, including the purchase and installation cost of a new machine, only accounts for 3% of the total life cycle cost of the equipment, and the remaining 97% of the cost is composed of electricity bills, equipment maintenance caused by downtime, and cost loss. For every 0.5% or 1% increase in energy efficiency, the savings are considerable. Yao Yedong said: "If you do a calculation, you will find that the higher purchase price is insignificant compared to the electricity cost savings. For customers, choosing ABB products, although the first purchase cost will be higher, But in the process of use, you can enjoy the benefits of efficient and reliable products, as well as perfect after-sales service.”
In addition to product technology, another core competitiveness of ABB motors is strong delivery capabilities. Yao Yedong said that ABB's advantage in delivery cycle comes from a mature product system on the one hand, and a strong factory operation capability on the other hand. Customers provide lead times that meet market expectations. Even in the special period covered by the new crown epidemic, ABB's high and low voltage motor products have never experienced delays in customer projects due to production stagnation, avoiding customer losses caused by delays, and presenting a satisfactory answer to customers.
Service: the whole life cycle, prevent problems before they happen
For mechanical equipment such as compressors and motors, service is as important as product. Therefore, ABB Motors has always been committed to providing full life cycle services for motors to help customers with operating costs throughout the life cycle of their equipment. Depending on the stage of the life cycle, ABB has different services to solve the problems that customers may face. For example, the installation, commissioning and extended warranty service of the motor after leaving the factory, provide original spare parts support for customers during the use of the motor, and have a professional on-site service team and a well-equipped workshop to help customers with on-site/return to the factory maintenance or emergency. Troubleshooting.
With the development of information technology, the needs of customers are constantly escalating, and ABB's requirements for itself are also increasing. For example, with the rise of the Industrial Internet and the Internet of Things, the compressor industry has blown up the wind of "building a digital factory and building an intelligent air compressor". As a global leader in the field of power and automation technology, ABB no longer passively waits to deal with the problems that will occur in the motor, but strives to use more advanced means to accurately identify the signs of problems in the early stage of failure, so that customers can plan Shut down for maintenance to eliminate hidden dangers in advance.
As we all know, predictive maintenance is carried out according to the actual operation of the equipment rather than the conventional schedule, which can greatly extend the service life of the equipment, reduce maintenance costs, and reduce losses caused by unexpected downtime. Based on the company's more than 100 years of motor manufacturing and service experience, ABB has accumulated a large number of motor faults and various models and algorithms. Through the development of digital series products, end users can benefit more from these valuable experiences. Therefore, as early as a few years ago, ABB started the research and development of digital products, and successfully launched products such as smart sensors, LEAP, MACHsense R, and forward-looking diagnostic tools, which can turn traditional motors into wirelessly connected devices, from the surface of the device. Measure key performance parameters and use this data to gain meaningful information about equipment condition and performance, letting users know when equipment needs maintenance, reducing the risk of system inefficiencies and equipment downtime, helping customers prevent problems before they happen.